Qualche tempo fa vi abbiamo raccontato come nasce uno pneumatico, quali sono i passi che lo portano dalla matita dei progettisti al cerchio delle nostre moto.
Come ci raccontava Salvatore, per passare dalla matita al cerchio uno pneumatico impiega 9 mesi. Tempo in cui viene progettato e testato a Milano per poi essere definitivamente collaudato sulle strade della Sicilia.
Dopo avervi raccontato la fase di collaudo, oggi vogliamo invece raccontarvi la fase di test indoor
Per farlo siamo stati a Milano nel piano -2 dell’headquarter di Pirelli, ospiti di Ferdinando Visconti Di Modrone e Guido Carosio che, come pazienti padroni di casa, ci hanno portato a curiosare in mezzo a banchi prova avveniristici dove vengono testati tutti gli pneumatici Pirelli e Metzeler. Dai PZero della Formula 1 alle Karoo4 che troviamo dal gommista.
Con Guido abbiamo percorso tutte le tappe di test che fa uno pneumatico appena disegnato dell’ufficio tecnico; primo su tutti la SGORBIATURA!
La sgorbia a molti richiamerà legno e foreste. Ma da queste parti è uno strumento con una punta affilata e riscaldata che anziché intagliare il legno intaglia la gomma di uno pneumatico slick ma con mescola e carcassa di progetto.
Per prima cosa, infatti, i tecnici devono verificare la funzionalità dell’intaglio ideato al pc dagli ingegneri. Per farlo abili artigiani ricreano gli intagli disegnati al laser sullo pneumatico liscio rendendolo appunto come quello di produzione.
Questo processo, apparentemente antico, manuale e artigianale, ha il grossissimo pregio dell’elasticità e della velocità. Creare uno stampo per ogni disegno da provare richiederebbe tempi e costi inutilmente elevati. Per questo ancora ci si appoggia alle capacità artigianali per avere in tempi brevissimi un nuovo disegno da verificare sui banchi prova.
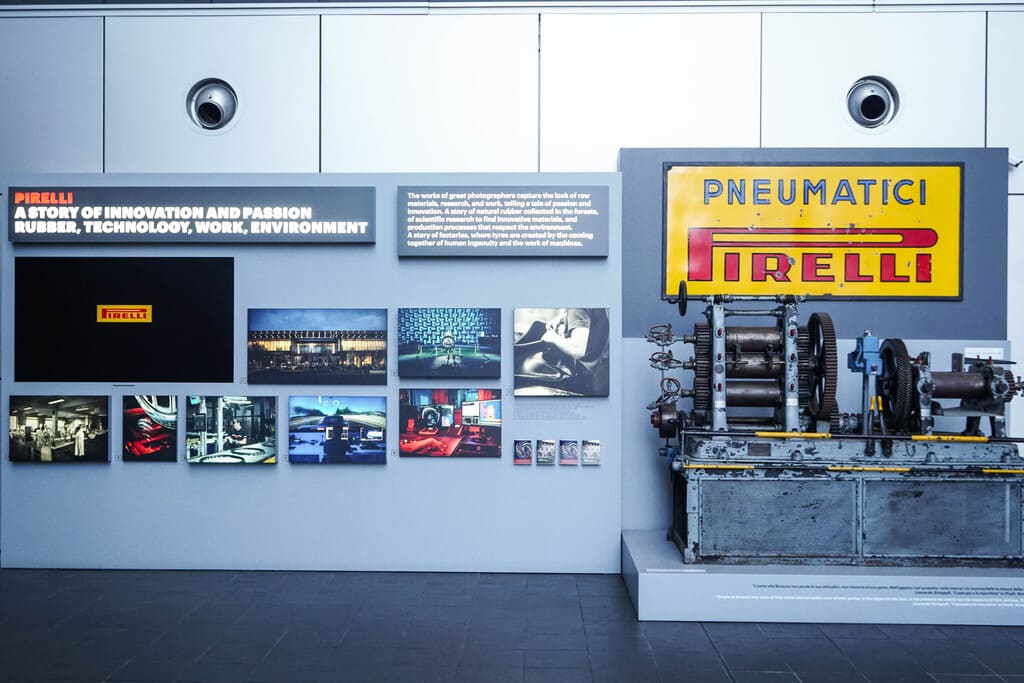
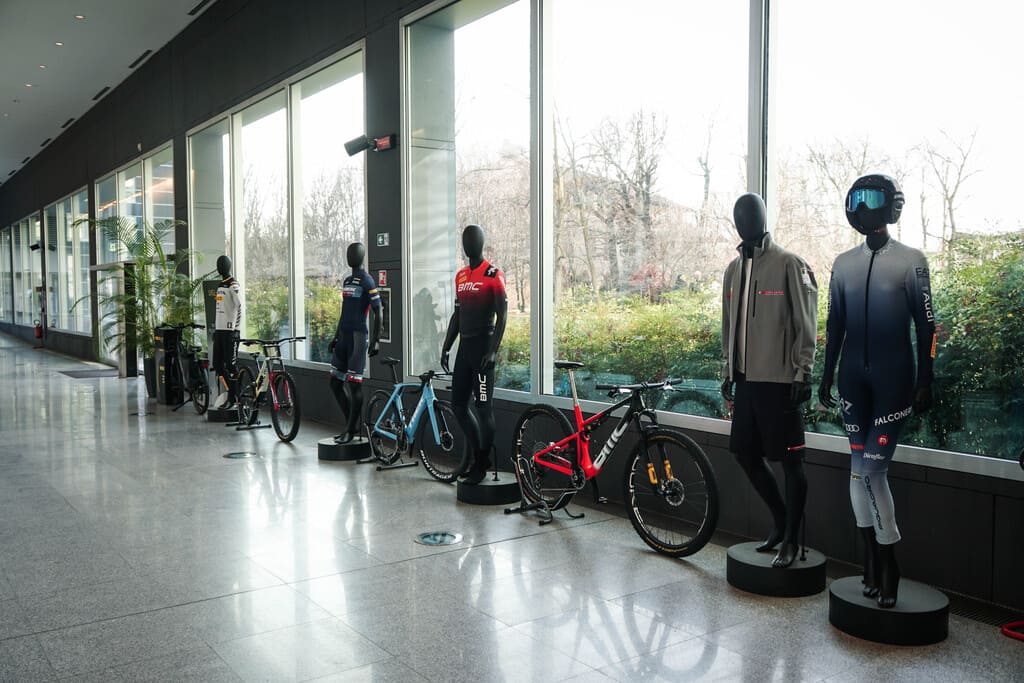
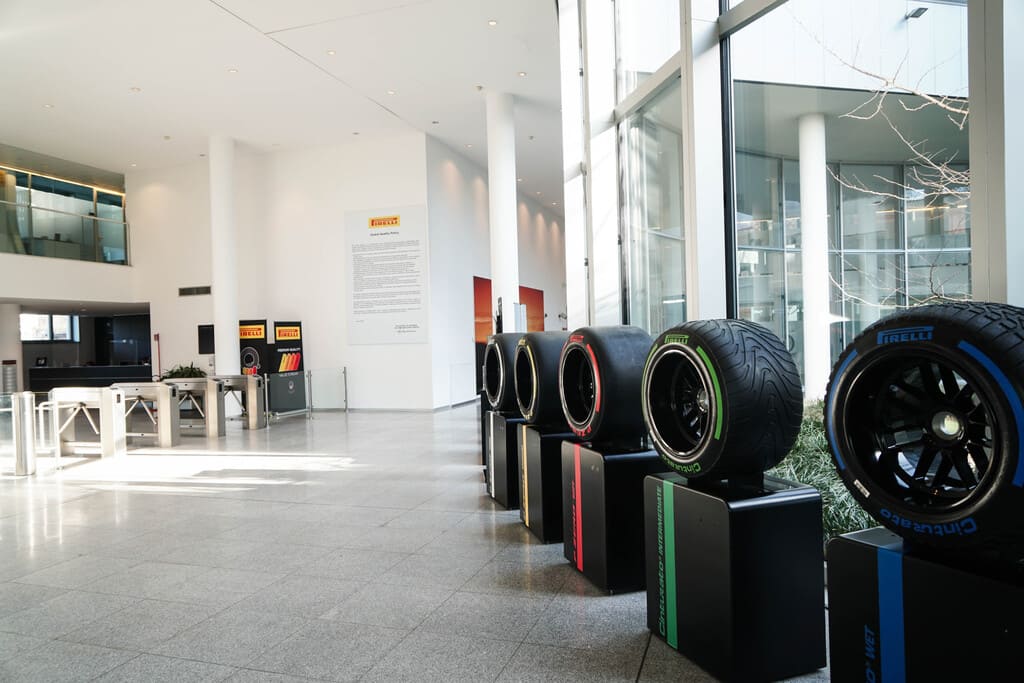
Una volta intagliato lo pneumatico va verificato dal punto di vista acustico perché i “vuoti” creati con la sgorbiatura introducono delle discontinuità più o meno marcate sul profilo omogeneo dello slick e questo crea rumore. Un rumore da quantificare per capire se sia ammissibile o meno.
Come suona lo pneumatico
La prova viene fatta in una camera semi-anecoica, una di quelle con le pareti tappezzati di coni di gommapiuma per evitare fenomeni di riflessione o riverbero del rumore.
Al centro della camera uno pneumatico viene messo a rotolare, trascinato da un tamburo rotante che ricrea l’asfalto che scorre sotto la ruota. Tutto intorno una miriade di microfoni di diversa tipologia misura l’emissione sonora decretando o meno la bontà del disegno.
Se, come ci aspettiamo, il disegno è approvato andiamo a mettere alla frusta lo pneumatico su banchi prova sofisticatissimi in grado di misurare la forza trasmessa dallo pneumatico all’asfalto in tutti gli angoli di piega e di manubrio.
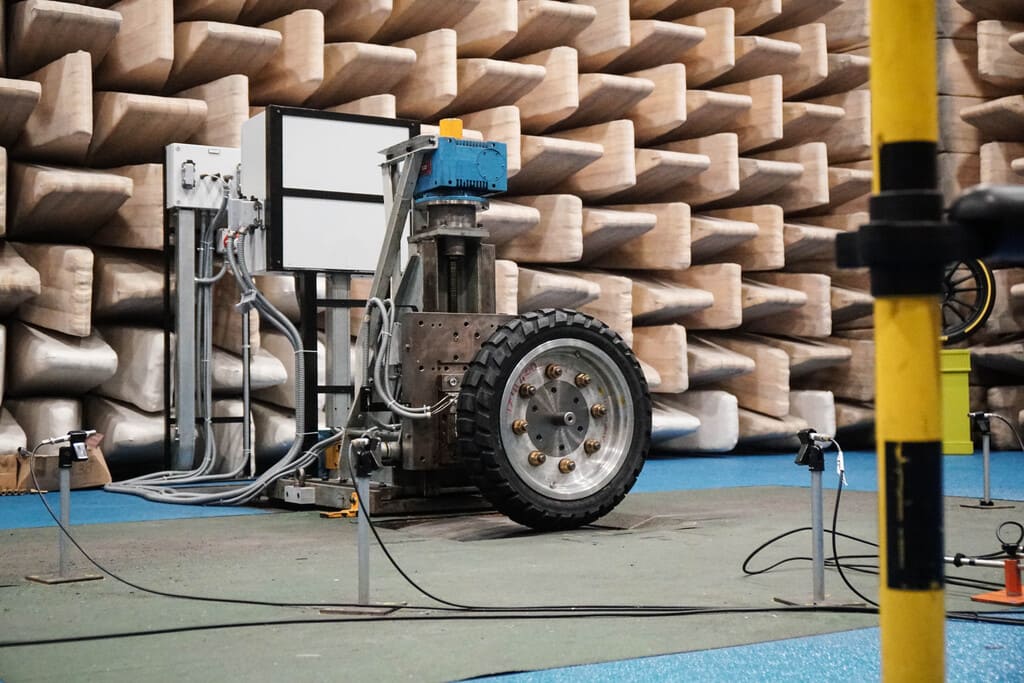
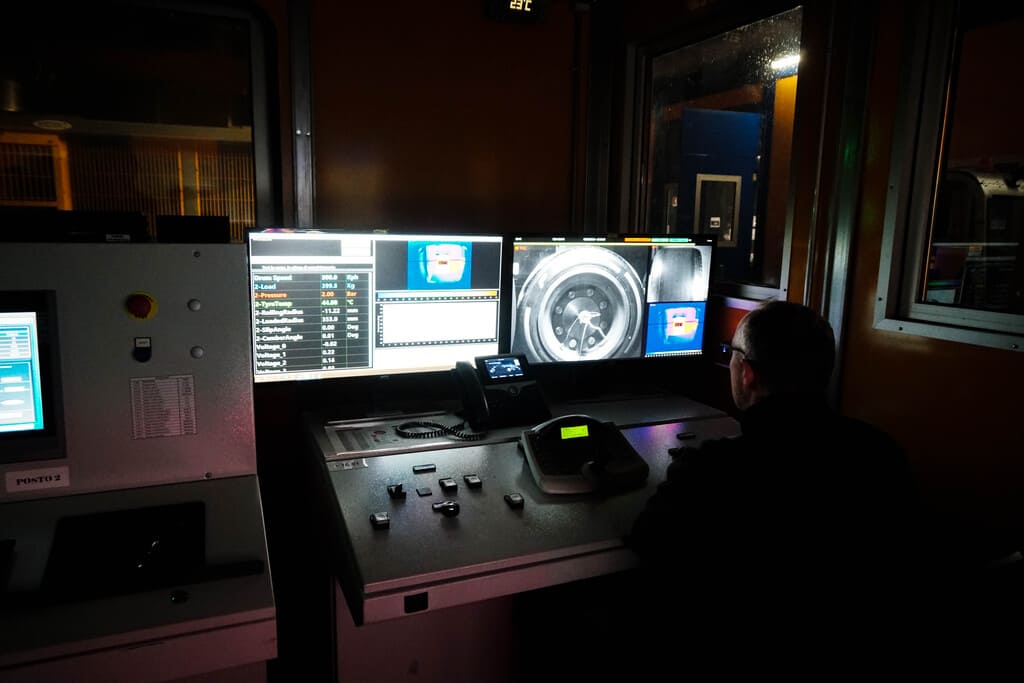
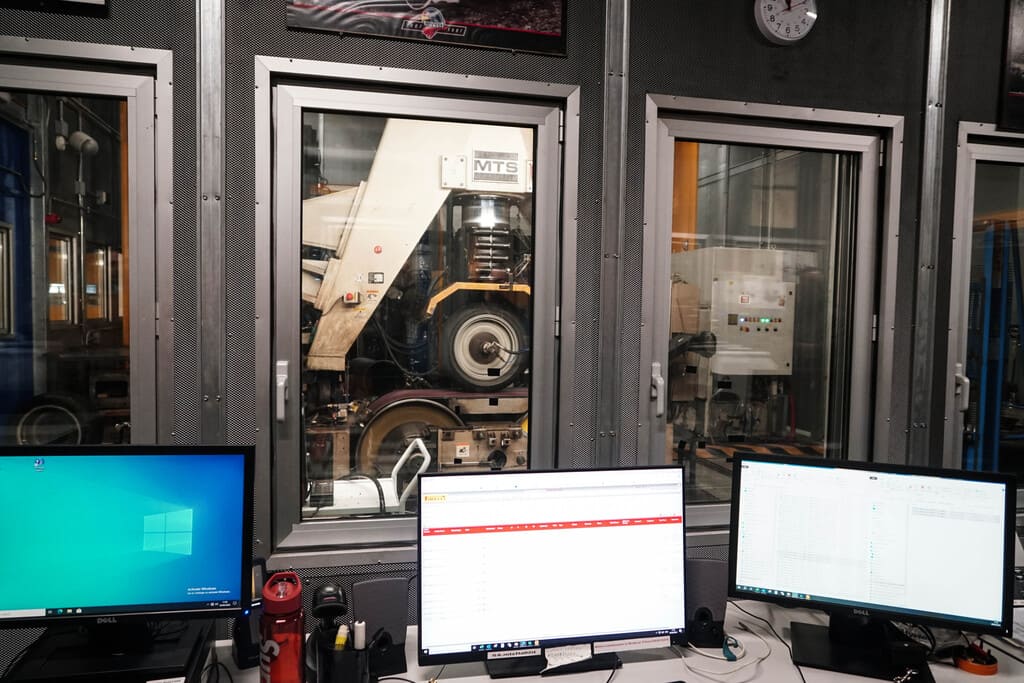
Con questi banchi si riescono ad avere condizioni totalmente ripetibili in cui neppure un Newton (o grammo) di forza può sfuggire alla registrazione e in cui possiamo paragonare scientificamente diverse soluzioni del trittico carcassa-mescola-intaglio velocemente e senza margine di errore.
Il test di percorrenza
Dopo aver misurato la performance, con altri banchi lo pneumatico viene letteralmente distrutto, con test di percorrenza dove viene lasciato rotolare giorno e notte al fine di misurarne l’usura chilometrica. Un test di fatica in cui viene stressato con colpi accidentali tipo buche o dossi per misurarne la durata su fondi severi. Poi viene messo al “banco alta velocita”, un banco in grado di portare lo pneumatico fino a 500km/h (velocità raggiunta solo per determinate applicazioni) per accertarsi che le carcasse, sottoposte a una severa forza centrifuga, non siano soggette a deformazioni particolari e che lo pneumatico non si riscaldi in modo anomalo.
Tutti questi banchi sofisticatissimi non possono sostituirsi al lavoro fatto dai ragazzi di Salvatore in Sicilia nel centro sperimentale.
A cosa servono i test
I collaudatori, soprattutto nel mondo moto, sono insostituibili, ma tutte queste prove e questi Stress-Test indoor, sono fondamentali in questa fase per tantissime ragioni; servono ad esempio a verificare i calcoli fatti dagli ingegneri, poterli validare in modo ripetibile e misurabile (cioè sempre nelle stesse condizioni e con dati non soggettivi) ma anche determinare il grado di sicurezza di uno pneumatico prima che un collaudatore o un acquirente lo monti sotto la propria moto
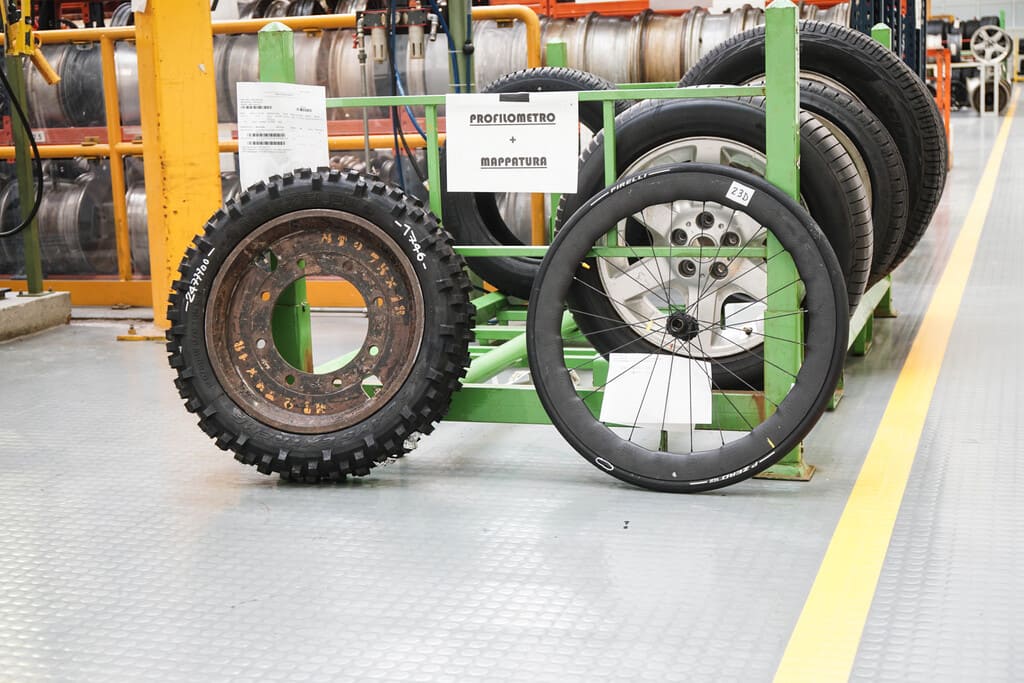
Quello di Milano è il centro prova unico di un colosso come Pirelli e Metzeler. Questo vuol dire che un Karoo4 o un Tourance Next 2 (come tutti gli pneumatici di gamma) sono collaudati sui medesimi banchi prova che hanno messo alla frusta gli pneumatici di F1 o della SBK e questo la dice lunga sulle performance richieste e verificate sui prodotti Metzeler o Pirelli che troviamo dal gommista.
Occhio però a pensare che sviluppare uno pneumatico di gamma sia più semplice che sviluppare uno slick estremo per una monoposto o una superbike!
Le competizioni infatti sono un banco prova formidabile e permettono di imparare come in nessun altro modo è possibile fare. Ma lo sviluppo di uno pneumatico con una coperta d’uso ampissima come un Karoo4, non è una sfida minore, anzi!
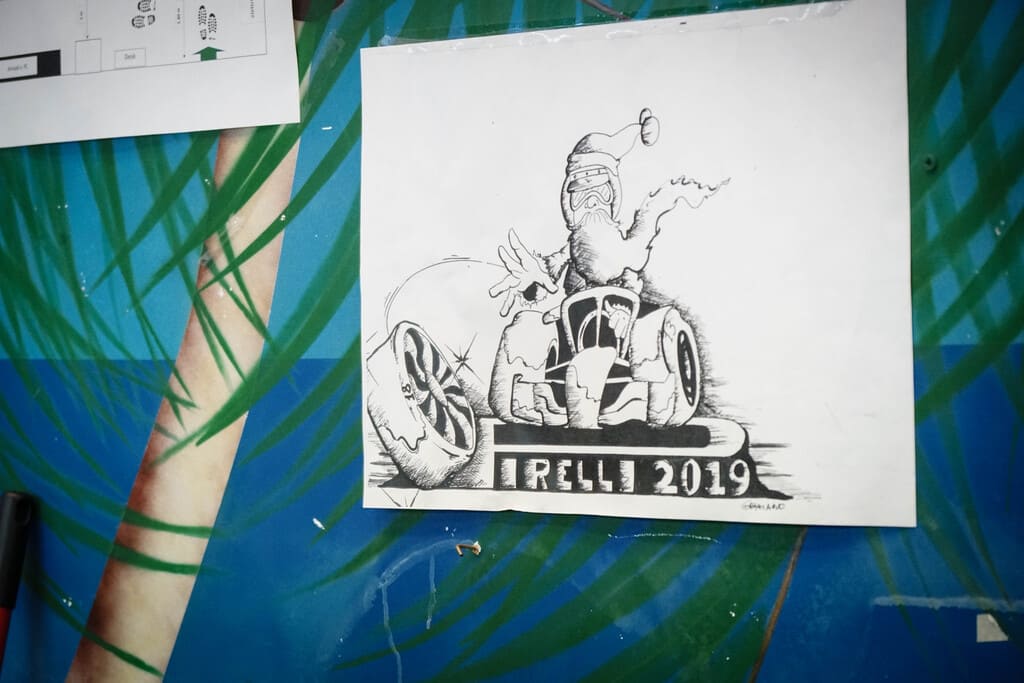
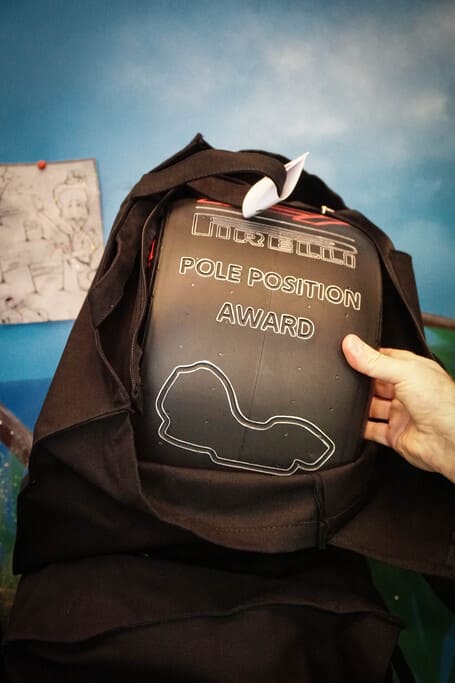
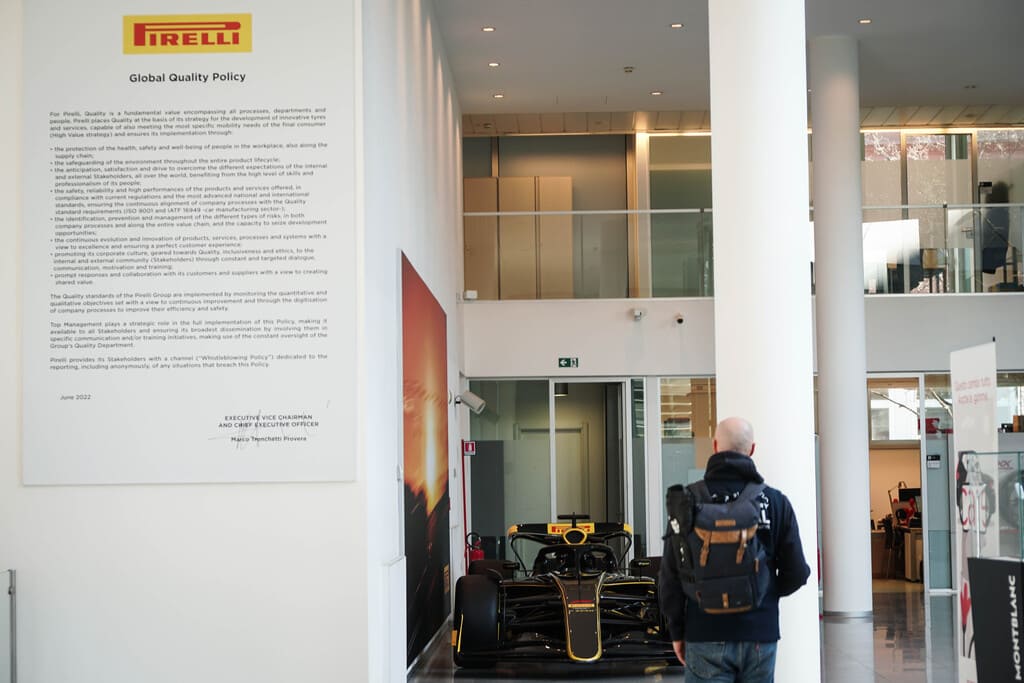
A differenza di uno slick che ha destinazioni d’uso estremamente strette e ben definite, uno pneumatico multipurpose deve infatti performare bene su ogni terreno. Avere la botte piena e la moglie ubriaca è una sfida che affligge l’uomo fin dagli albori della tecnica.
Testo: Dario Lupini